We have a close working partnership with each of our factories - only working with those who share our commitment to the human rights of every worker. LS Manufacturing is a family-run business based in the West Midlands, established in 1957 by the father of the current chairman. A door-to-door salesman during the weekends, he worked in a foundry during the week, whilst his wife would cut and sew the garments at home. From these humble beginnings, the business expanded to its peak, employing over 150 people at its manufacturing facility in Wolverhampton. The third generation of the family are now involved with the business and we spoke to Heidi Humphreys, the Head of Technical, who oversees all production.
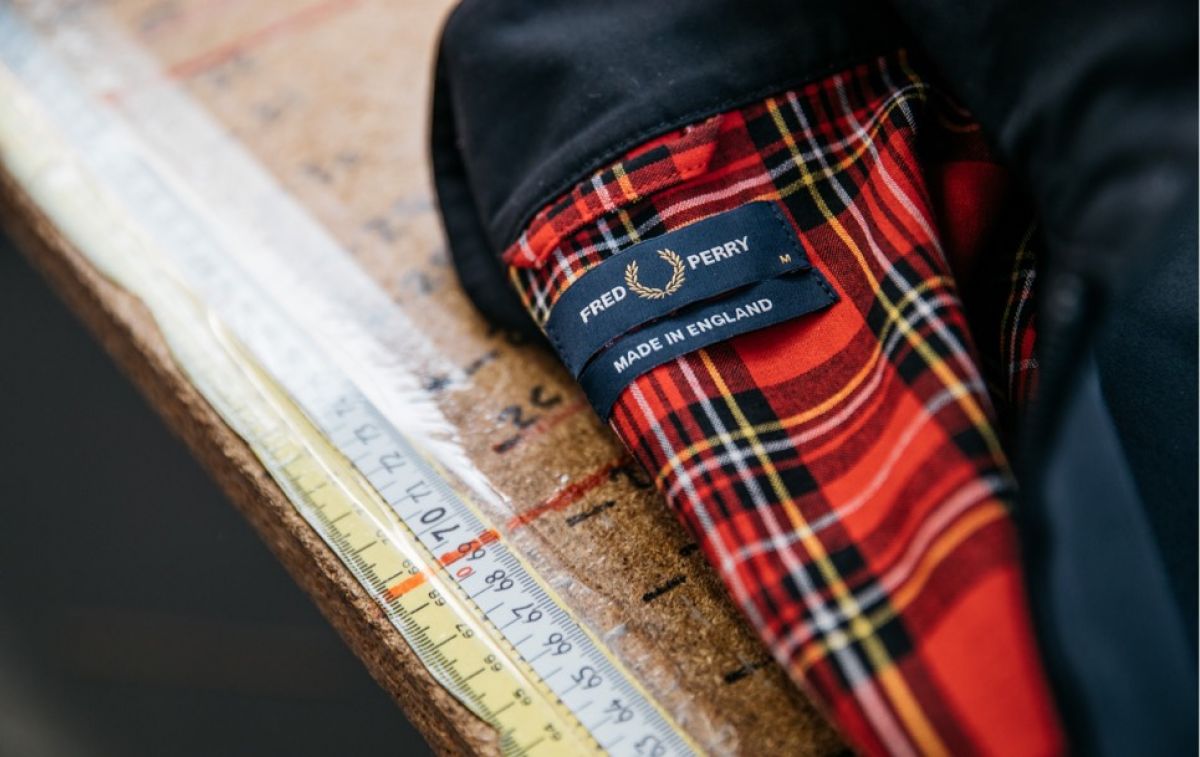
Made in England -
The Tennis Bomber &
Harrington Jacket
Photos by Chazz Adnitt
We visit LS Manufacturing, who we have worked with for 14 years, to showcase their expertise and innovation whilst making our Harrington and Tennis Bomber jackets.
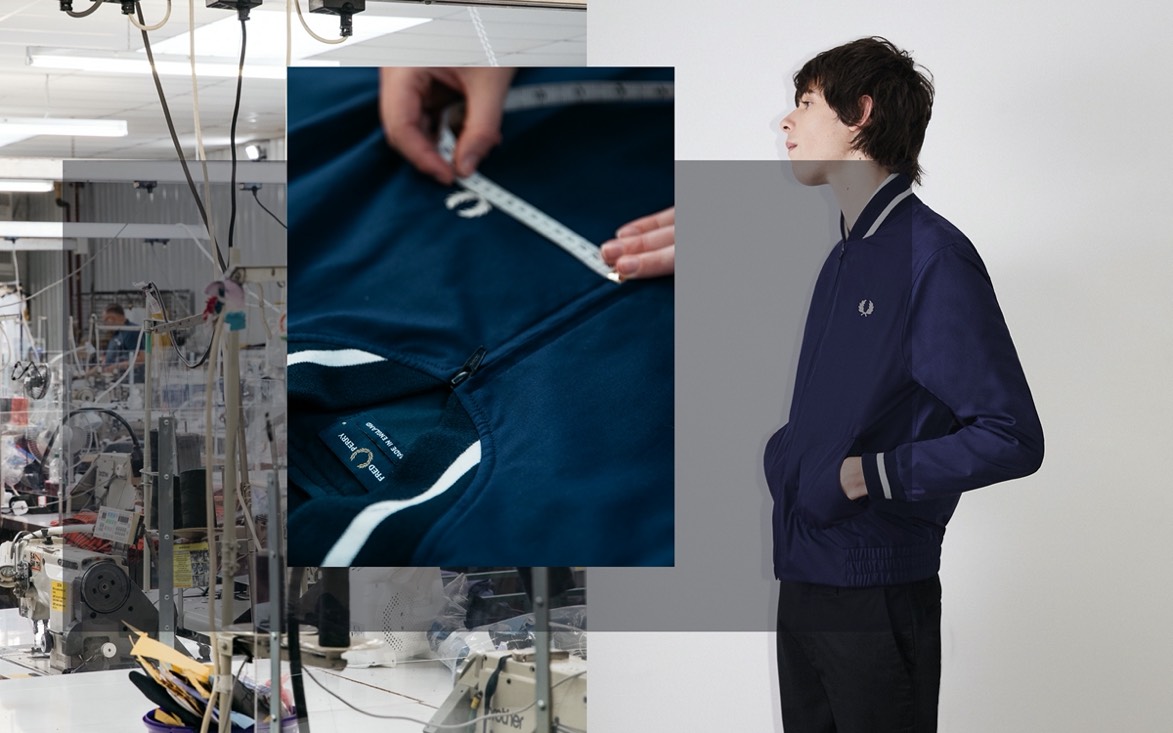
LS Manufacturing still retains a strong family work ethic which extends to our warm and strong relationships with both staff and customers. We have managed to build a reputation for quality and innovation. At its peak, the clothing industry in Wolverhampton boasted over 250 clothing factories in the borough. The current figure is around 5. We are proud to have survived the challenges in UK manufacturing and that we have such strong relationships with staff and customers alike.
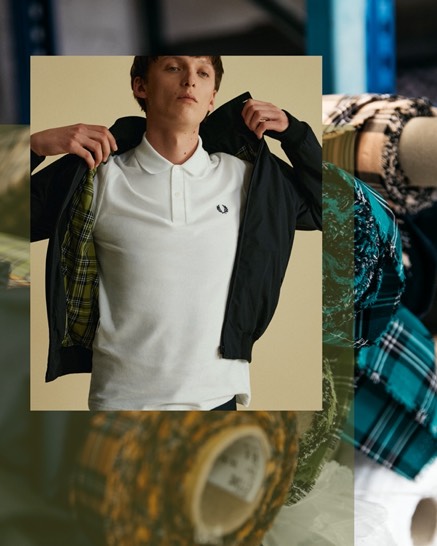
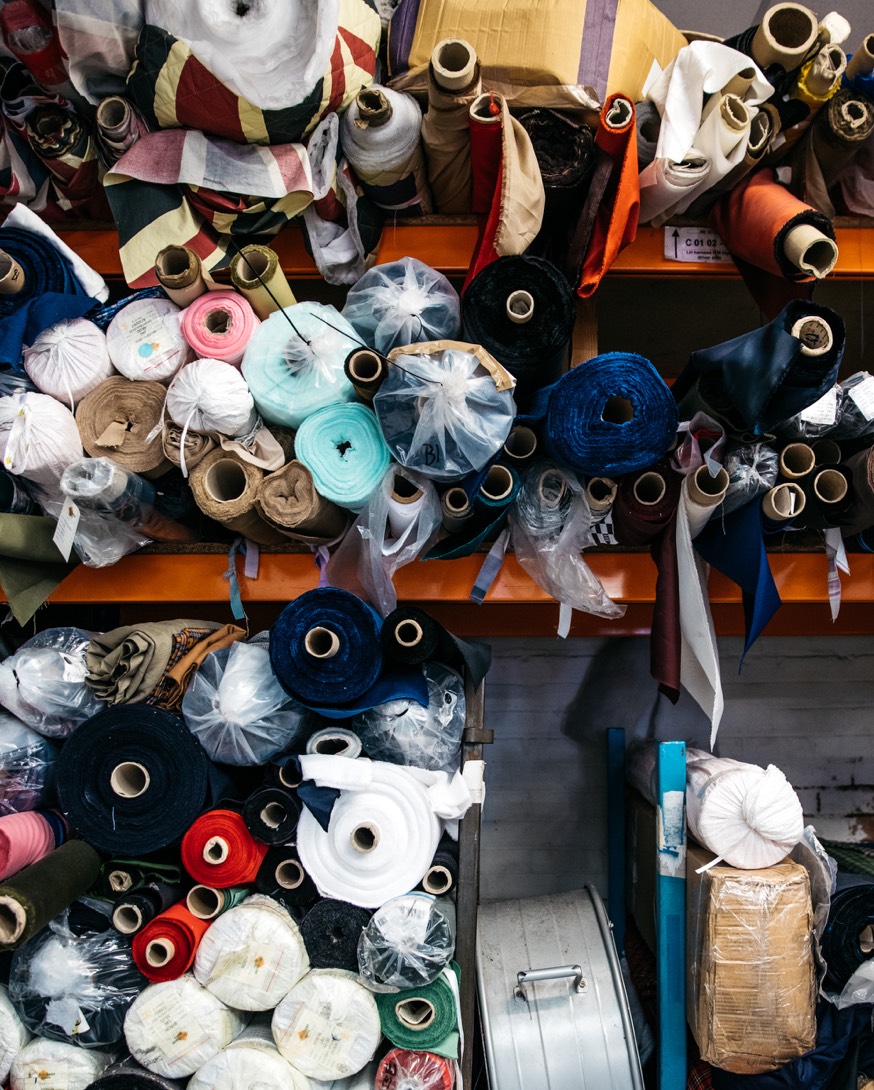
We currently have 70 people in the team made up of extremely loyal staff who are resilient to changing times. Each team member is highly skilled and close knit, they are always on hand to support each other – a number of staff started with us at sixteen years old and are now in their late 50s.
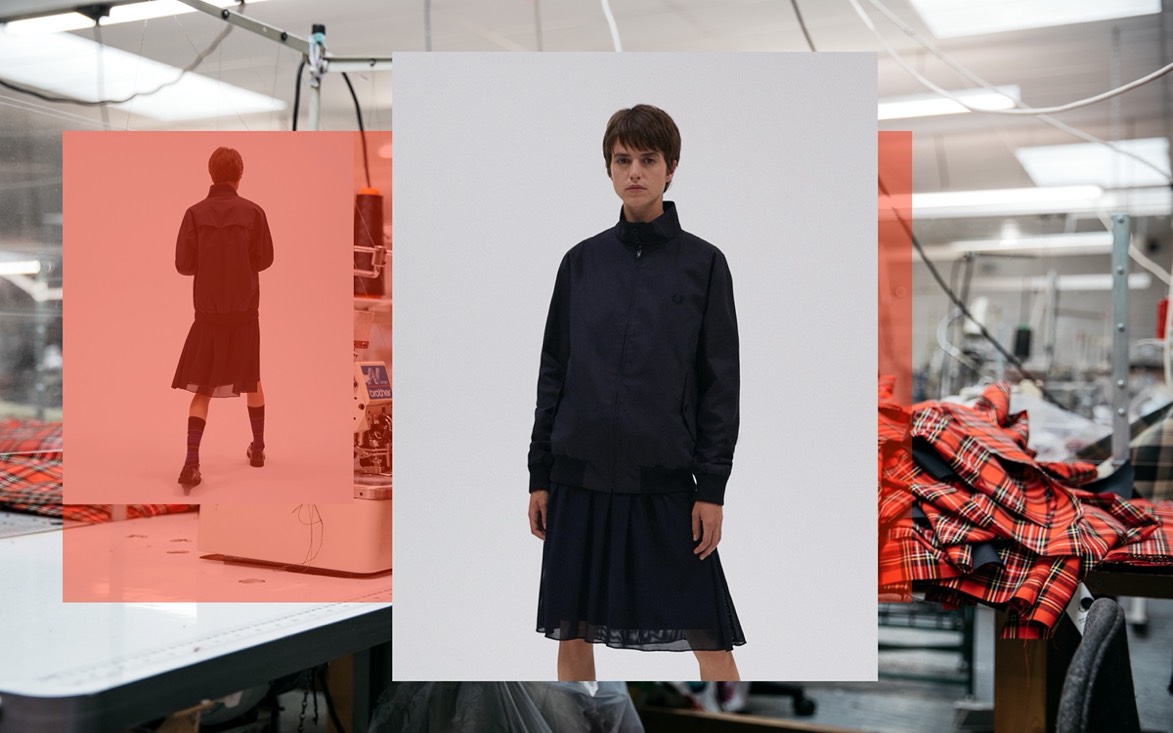
Once the fabrics, components and designs have been selected by Fred Perry Head Office, we at LS will then create the patterns and grade them for the various sizes. From there, we will produce a red seal sample to ensure that the fit is correct and the drape is up to Fred Perry standards. As soon as this is approved, we will create a gold seal sample. This sample is then followed throughout the production process. The first part of production is to create the markers on our digital CAD system, which are used to cut the garments. Whilst this process is under way, the fabrics are sent away for testing. After the fabric has been cut, certain parts are fused and others sent to the embroidery room to have the Laurel Wreath embroidered onto the left chest. The next step is for the fabric pieces to be fed onto the production line. Each machinist will sew a small part of the garment and pass it onto the next person. The buttonholes and buttons are attached once the garment is fully sewn and the finished garments are given a final press and full inspection. Garments are meticulously inspected whilst going through the packing process. Before leaving, the goods then go through one final review, ensuring every garment is of the highest quality standard. A real labour of love.
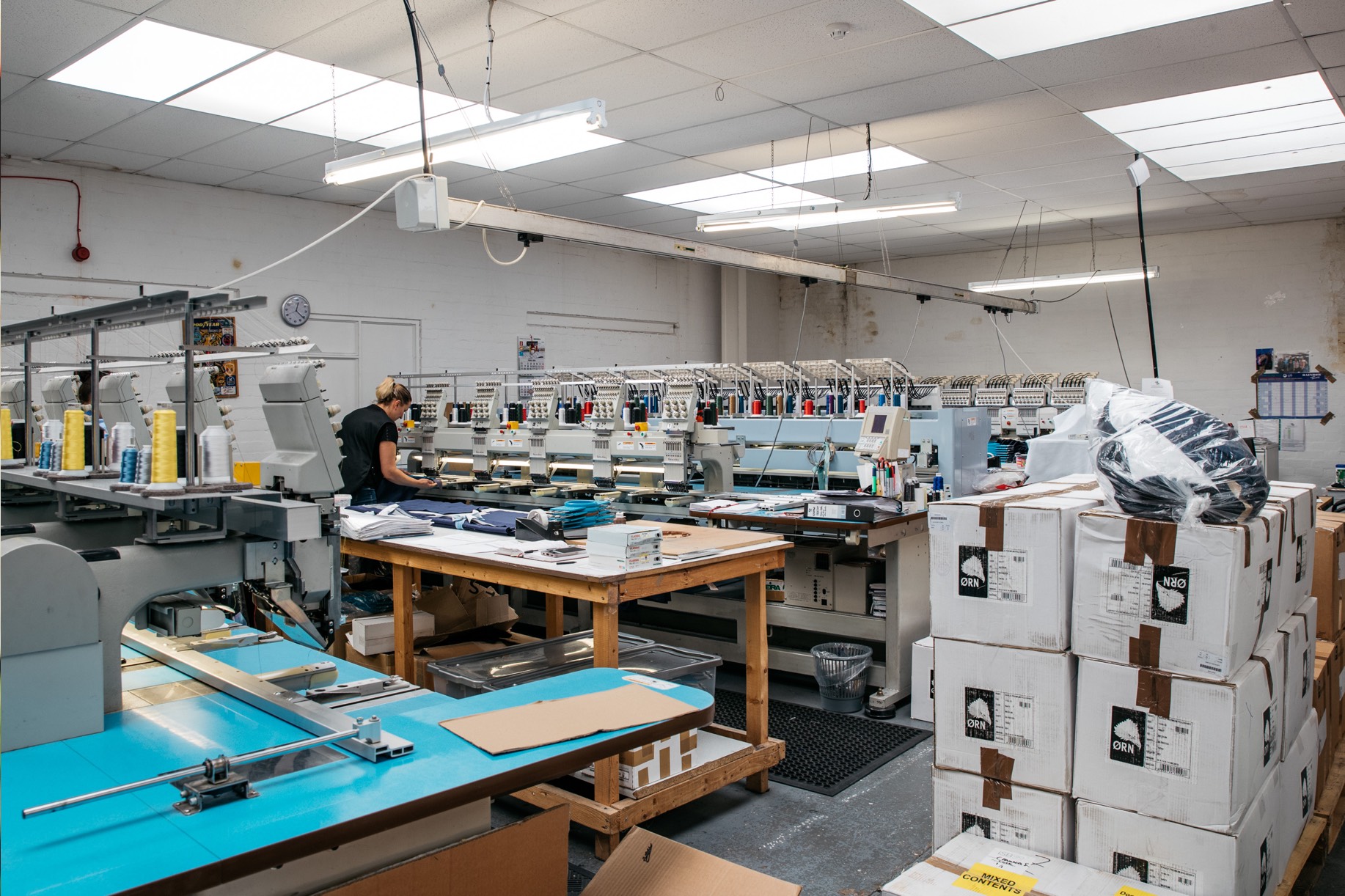
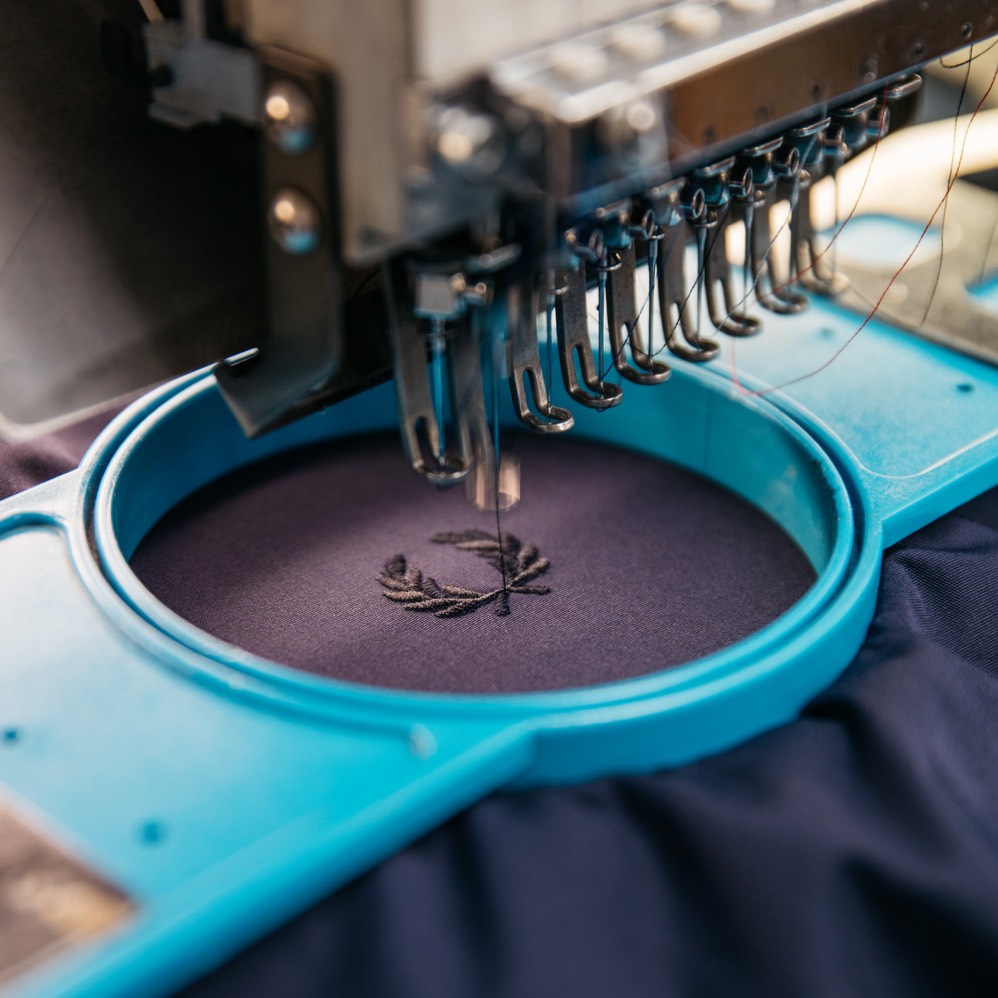
Both of these iconic garments are cut and sewn in our factory in Wolverhampton, they are all made with the best quality fabrics money can buy. Some of the oldest records show that in the 1970s -1980s, the factory was manufacturing Harrington jackets, and fifty years later, they still are producing the same garment. They are British made with an emphasis on the quality. The garments are timeless and iconic… and made to last! They have a unique look and are an investment for the future, not just for today.
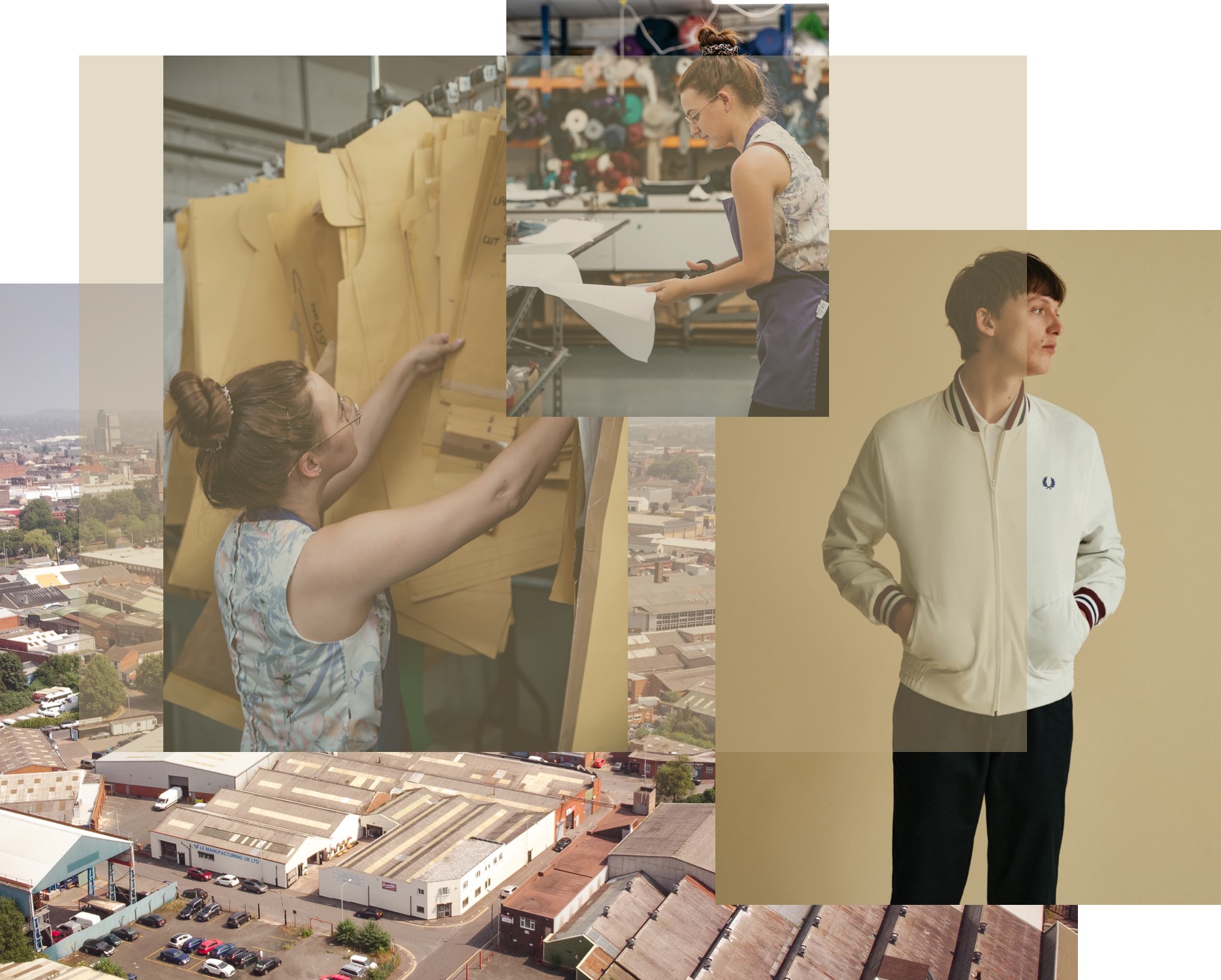